Furnishing quality
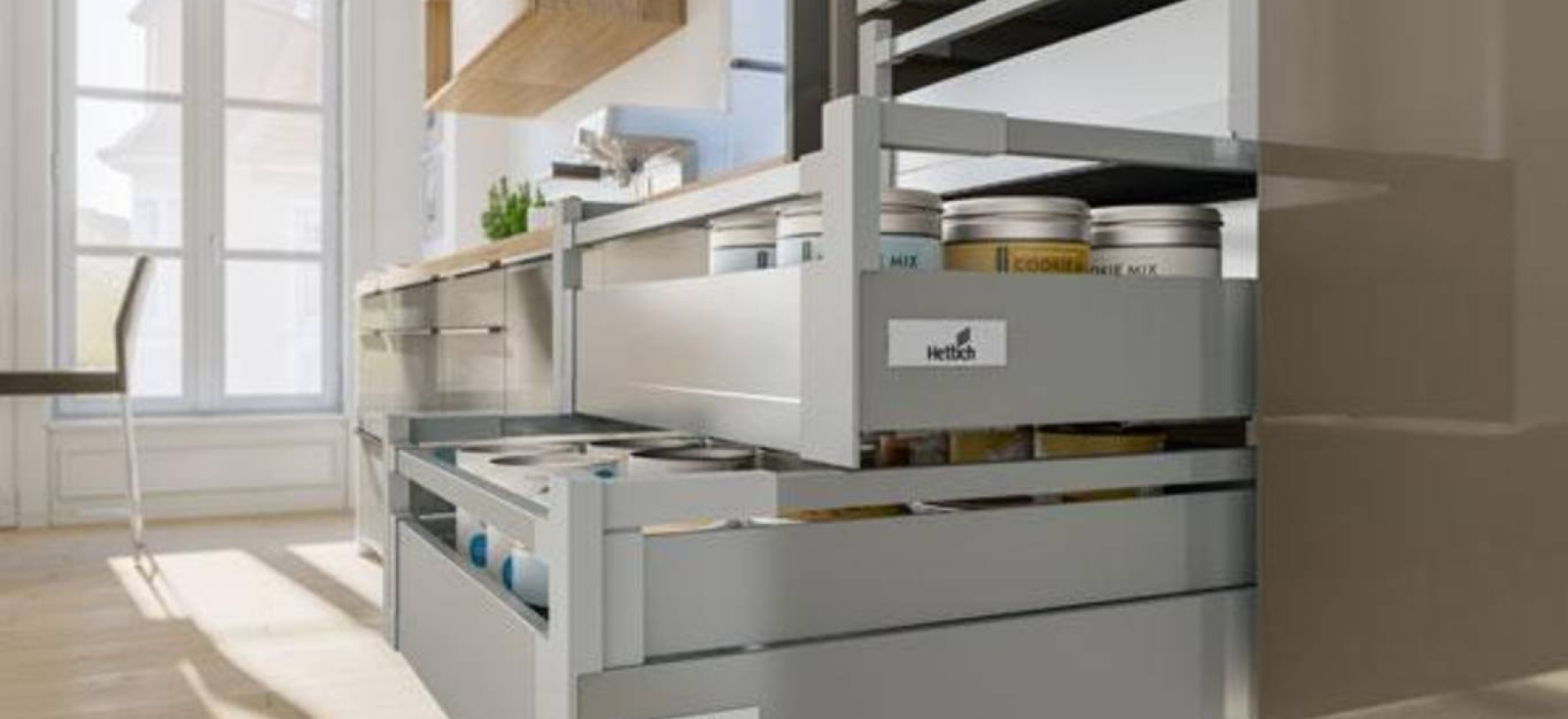
The doors, flaps and drawers of a new kitchen are most likely fitted with quality hardware by Hettich. The company was founded in 1888 and is regarded as the leading maker of furniture fittings for the living and working area. Since 2018, FIEGE has been handling the storage, the building of set kits, as well as the labelling and shipment of drawer systems for the Hettich Group at its location in Melle – where it has also been able to continuously increase efficiency.
Looking for more productivity
Eugen Brossart was given a clear mission. “We were looking for a new partner for our logistics, packaging and shipping that would increase both quality and efficiency,” says the Head of the Packaging Profit Centre of Hettich Group. The thought behind this was simple: Hettich was looking to focus exclusively on its core business, which is the production of quality fittings for furniture. Logistics was consequently outsourced, and FIEGE became the partner of choice. The good value-for-money ratio was particularly convincing, Brossart tells us.
The shared search for a new site led the companies to the city of Melle in Lower Saxony, around 30 kilometres from Hettich’s headquarters and production site in Kirchlengern in East-Westphalia. That was in September 2018. After that, things took off quickly. Brossart sums things up: “FIEGE was incredibly fast in ramping up the entire project including the operation of a specially leased property as well as its shelving. Only three months later, operations went live with 15 different sets to begin with.”
Collaboration digitized and expanded
Today, a good three and a half years later, what was once 15 set variants has become 67, which are destined for customers in Central and Southern Europe. “The entire team has constantly developed and independently found solutions to continuously improve performance and quality management,“ explains Brossart. Completeness is always the top priority. “If a part is missing, the drawer system cannot be assembled. However, we only notice this when the packages are unpacked at the customer's premises. Reliability is the be-all and end-all, process reliability must be right - and at FIEGE it is.“
Every day, 6,000 Hettich parcels leave the assembly line in Melle, FIEGE has digitalized its quality management, and inspections are carried out using a tablet instead of a clipboard. "We can be really proud of what we have achieved together," says Brossart, who also recalls some tricky moments. “The yellow vest protests in France and, of course, the recent coronavirus crisis were difficult situations. But we overcame them.“
New challenges
Brossart can therefore claim to have fulfilled his original brief. Nevertheless, he sees no reason to lean back, and in the cooperation between Hettich and FIEGE, the next order is already just around the corner. “We will soon be starting a pilot project,“ says Brossart, “in which the drawer system will be fully assembled using an automated machine, then packed and shipped.“ As they say, you should never stop improving.
Looking to become more efficient?
We know how to help!