Lean-tastic company
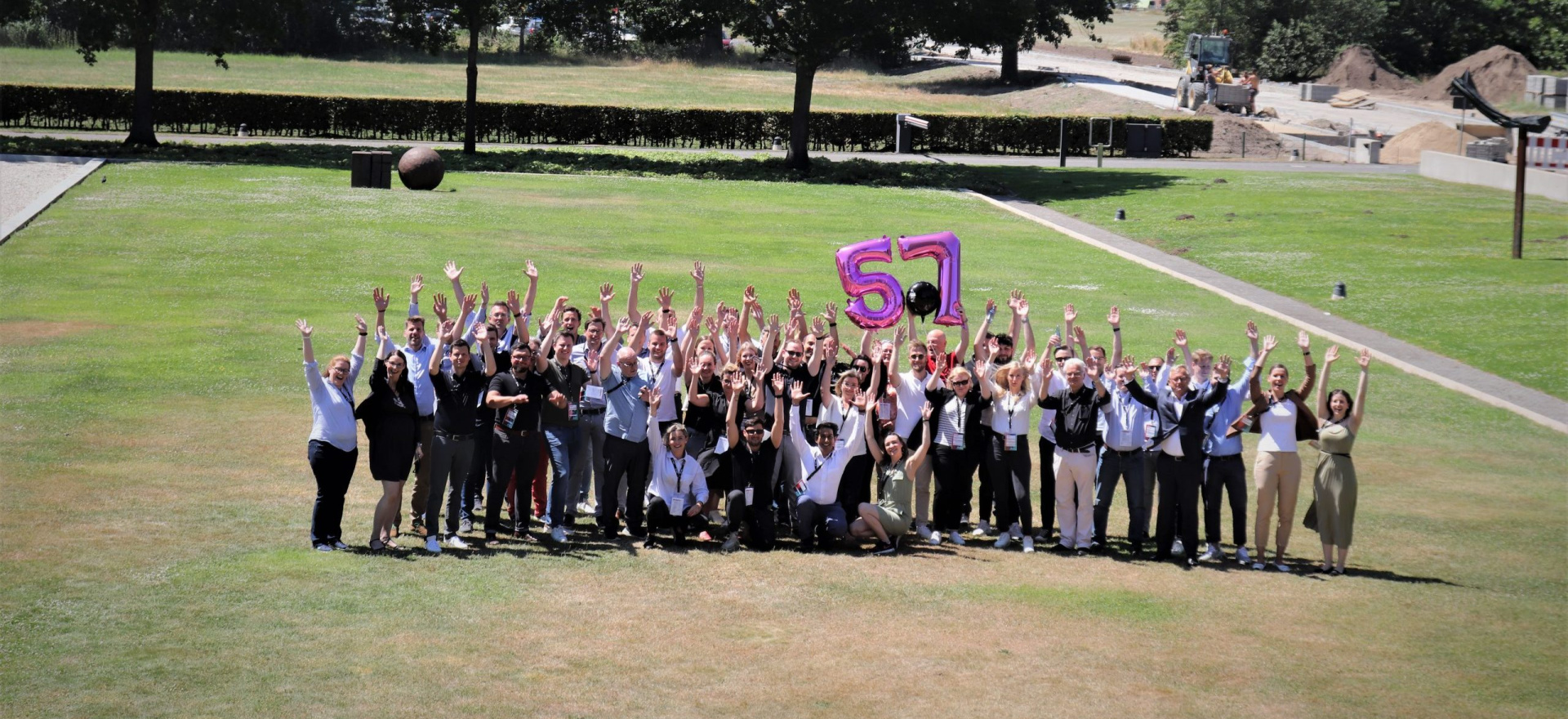
5.7 million euros – that is the amount that FIEGE has helped its clients save with optimisation projects that were rolled out in 2021. Lean Management is the magic word on the way to greater improvement and less waste. In this interview, Maj-Britt Pohlmann, Director Operational Excellence, and Franziska Hedtkamp, Lean Manager FIEGE Group, talk about the first-ever Leantastic event held in the history of FIEGE, but also about challenges and an “unstoppable wave”.
THE FIRST-EVER LEANTASTIC EVENT IN THE HISTORY OF FIEGE WAS HELD IN THE MONTH OF JUNE OF THIS YEAR. THE EVENT TOOK PLACE ON THREE DAYS – AND LEANTASTIC SOUNDS INDEED LIKE SOMETHING OF A FESTIVAL. BUT WAS IT REALLY A FESTIVAL?
Franziska: It did very much feel a bit like a festival. It was a good mix of networking, an exchange of knowledge and Best Practices, the gathering of impulses for future improvements and a little about gaining a broader perspective on things and boosting enthusiasm for Lean Management. The highlight was the “self-composed music” – that is the internal lean fair, where each branch presented it’s respective lean activities and optimisation projects and all participants were able to take home new ideas.
Maj-Britt: The festival feel came mainly from the vibes that were almost palpable. Our participants came to realise: FIEGE has an international network of many like-minded people who are passionately dedicated to the subject of Lean Management and can achieve a lot together.

Franziska Hedtkamp, Lean Manager FIEGE Group.
AND WHAT CONCLUSION DID YOU DRAW?
Franziska: We have triggered something of a Lean Management movement here at FIEGE and the network offers a huge wealth of knowledge. The Leantastic event showed us where we are today and what we have already achieved. But we also took a closer look: What are the next steps within the operational and administrative segment? Which new technology can we trial in future?
Maj-Britt: The human factor is also key for success. We have incredibly great Lean Managers from a range of different countries who contribute a great deal of individuality and diversity: men and women, more mature and younger colleagues, with or without a degree. Those are the people who set our company in motion. This wave will carry more and more people along and make FIEGE a constantly improving company.
MAJ-BRITT, YOU HAVE BEEN WITH FIEGE SINCE 2020 AND TODAY YOU ARE DIRECTOR OPERATIONAL EXCELLENCE. WHAT HAS HAPPENED THESE PAST TWO AND A HALF YEARS WITHIN LEAN MANAGEMENT AT FIEGE?
Maj-Britt: When I joined FIEGE, we were still at the starting stage. The team was comprised of 20 colleagues back then who had just successfully completed the first projects. Today, we have over 70 allies and have implemented Lean Management at 92 locations and further professionalised our methods. Last year, we rolled out over 100 optimisation projects which helped to save 5.7 million euros for our clients. Every time we trigger something, its success becomes measurable. The topic is set within FIEGE and is on its way to being anchored in everyone’s mind. We created this foundation, and I am very proud of this.
FOR ALL THOSE WHO ARE NOT YET THAT FAMILIAR WITH THE TERM LEAN MANAGEMENT: WHAT ARE YOUR TASKS WITHIN THE COMPANY, AND WHAT ARE YOUR GOALS?
Franziska: Lean management is a philosophy of continuous improvement. It is about optimising all process flows within an organisation. And this requires the right mindset, a special understanding of leadership, a modular set with different methods and Best Practice sharing. We want to shape FIEGE into becoming a lean-thinking and lean-acting logistics company. It is our goal to empower every single employee – from intern to department head – to question our processes and structures, to spot potential optimisation and to initiate change. That is why we motivate our colleagues to ask themselves this question every morning: What can I improve today?
IT IS ALWAYS POSSIBLE TO MAKE SOME SORT OF IMPROVEMENT. DOES A LEAN MANAGEMENT APPROACH EVER END?
Maj-Brit: That is a definite no! One Lean principle is to strive for perfection – that means there’s always something to improve. This does not require the perfect solution right from the start, but rather the art of small steps. It is better to improve one percent a day than never getting to 100 percent. As the market and the technological environment change ever faster and challenge us with new demands, it is all the more important to be able to react agilely with process changes. Lean impacts all processes at our company – from warehousing to transportation to key administrative processes.
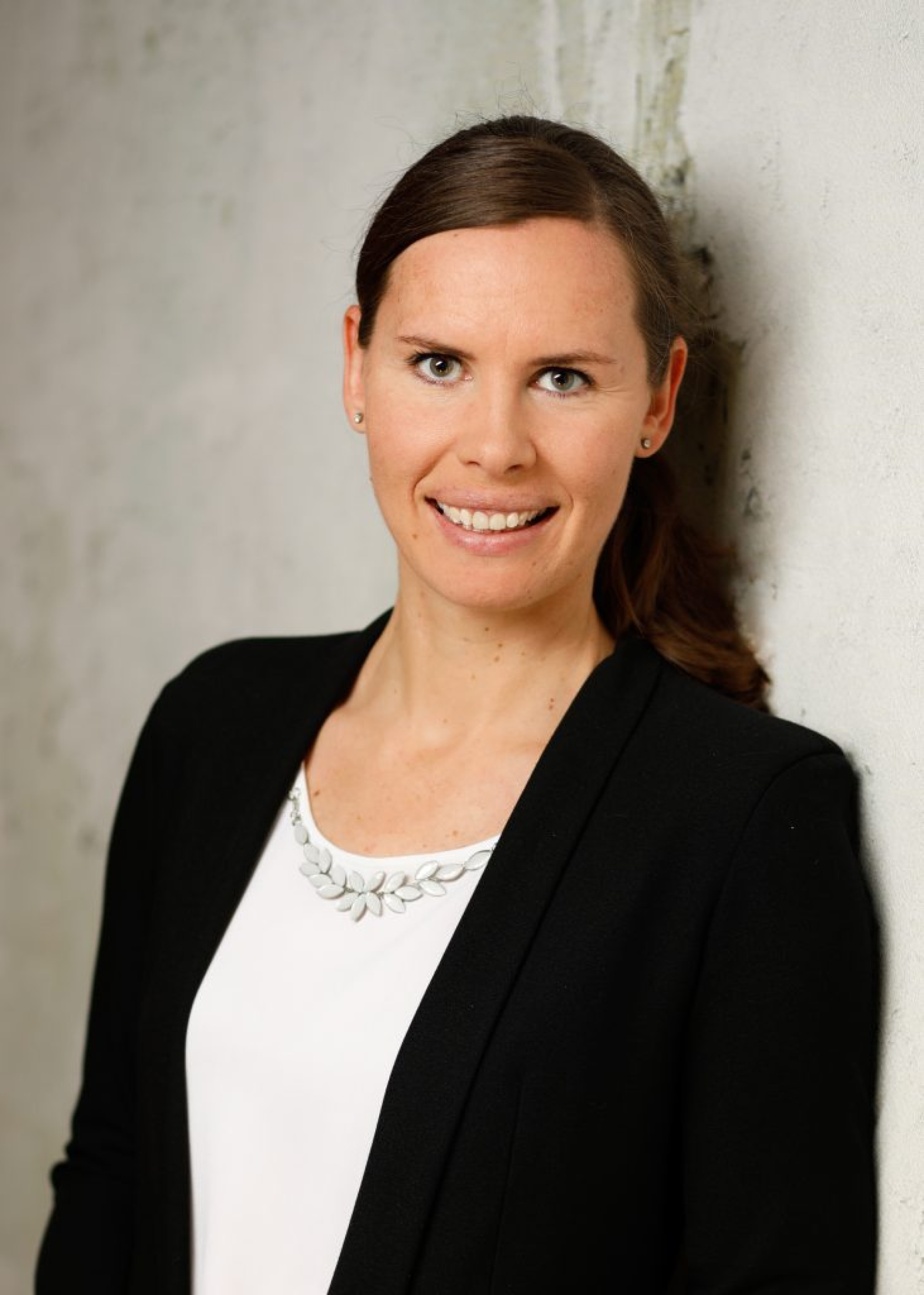
Maj-Britt Pohlmann, Director Operational Excellence.
AND DO YOU SOMETIMES HAVE TO OVERCOME OBSTACLES?
Franziska: One of the biggest obstacles is this sentence: “We have always been doing this like that.” After all, here at FIEGE, we have many employees who have been working with us for a very long time and contribute an incredible wealth of process expertise, so this is completely understandable. Therefore, it is particularly important to us that everyone involved is sensitised to our activities and that we establish a culture of asking questions. The message is: When we create improvements, they become the new standard and if not, we simply try something new.
WHICH ROLES DO INNOVATION AND AUTOMATION PLAY?
Maj-Britt: Those topics are extremely relevant for us, especially when it comes to the imminent steps. Under the umbrella of Operational Excellence, we at FIEGE bring together all areas that are key for our process structure such as Engineering, IT, Quality and Lean Management with representatives from the operations to raise our organisation to the next level. Our colleagues from the Business Units know exactly where we still have pain points in our own processes today and what new challenges are driving our customers. This leads to strategic fields of action in the areas of automation, digital process solutions and process excellence, for which we create solutions and take them to the roll-out in a structured way. Piloting new technologies plays a central role in this. Our Engineering and IT teams are constantly screening the market to identify new technologies that support our process goals. All of this pays towards achieving our company-wide roadmap to process vision 2027 – which creates competitive advantages for our customers and a pleasant and structured working environment for our employees.
WHICH SPECIFIC MILESTONE HAVE YOU ALREADY ACHIEVED AND WHAT IS NEXT IN LINE?
Franziska: We initially focused on the operational area. This is where core operations take place and the need and therefore also the potential are especially large. With Accounting, we are now also addressing a first administrative department. We were able to successfully conclude the pilot in the first half of the year and will soon focus on the People&Culture department. Thus, the central service functions will gradually be activated and next year the Lean Managers of each branch will be trained so that they can include the administrative areas. We want to reach our whole company with Lean Management.
Maj-Britt: I am focusing on the further development of our Operational Excellence Initiative. By the middle of next year, we want to have already set the first accents in the areas of warehouse automation, digital process solution and process excellence. We are making our company “Fit for Future”.