Road to Automation
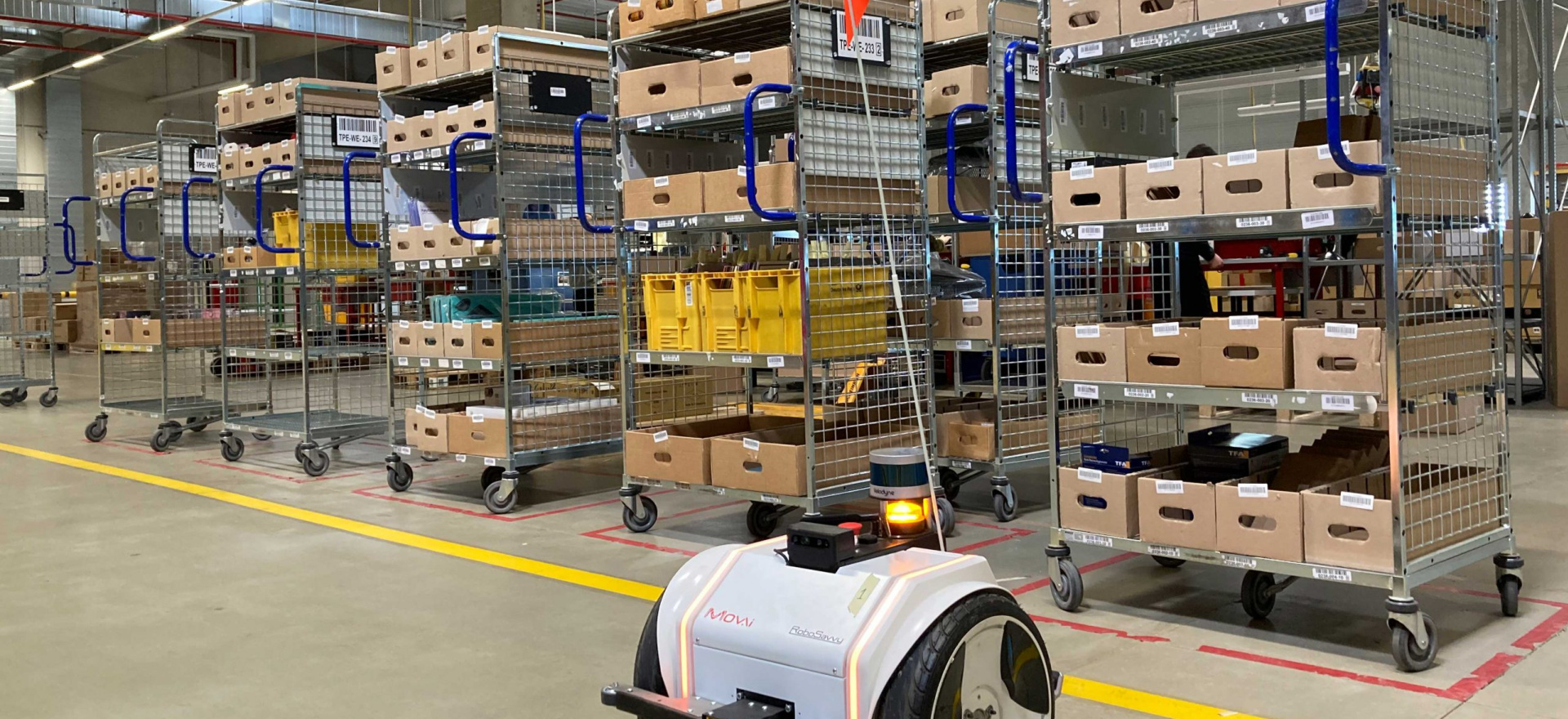
At the FIEGE location in Greven-Reckenfeld, two Autonomous Mobile Robots (AMR) assist with the storing of small items.
One can be forgiven for thinking that Segways have made themselves at home at the Fiege Mega Center in Reckenfeld. On closer inspection, however, it becomes clear that the two cobots are actually the TUGBOT, an AMR developed by RoboSavvy and running the MOV.AI Robotics Engine Platform. The two mobile robots handle the automated transportation between two disposal points of picked electronics. Following a successful four-week pilot, Fiege has now added two TUGBOTs to the team.
Difficult beginnings
Initially, however, things did not look as if it would work out. “We first met RoboSavvy and MOV.AI a good two years ago via WAKU Robotics, one of our partners on automation projects”, as Jens Veltel from Fiege Engineering recalls. Even though interest in the TUGBOT was considerable from the very start, a first pilot failed to materialise. “Back then we realised that the technology was not quite up to being efficiently integrated into our warehouse operations”, Veltel says.
One of the reasons for this was that Fiege Engineering requires tests like these to work completely self-sufficiently with its own systems without any ties to the manufacturer’s systems. “Our goal is to gather experience and develop an ever-greater feel for robotics. That explains why we not only analyse the technology, but most and for all if and how it would work within the World of Fiege”, Veltel explains further.
Flagged for follow up
Although the first test was not crowned by success, Fiege did not take this as a reason to break off contact with RoboSavvy and MOV.AI. Rika Voß, Fiege Engineering, explains: “Once we believe in a certain technology, we do not let setbacks discourage us. We simply give the entrepreneurs more time to improve their development.” The robotics experts were thus invited to a further Proof of Concept (PoC) in August of last year.
And this time, the TUGBOT and MOV.AI met expectations. It reliably manoeuvred the picking trolleys in alternating directions on a roughly 100 metres-long stretch. This stretch is located on the upper level of the two-storey building in Reckenfeld where the small cobots collab with pallet jacks and humans. “The coupling was specifically printed using a 3D printer so in principle, any system can be hauled”, says Voß.
Integration into standard operations
Since processes ran smoothly, Fiege decided to buy the two AMR and also gave them nicknames, as the key user in charge at the Greven-Reckenfeld location, Kevin Stulert tells us: “We call them Adam and Eve as they are the first of their kind here. By now they have covered some 700 kilometres each.” For now, the TUGBOTs receive their orders manually but it is conceivable that in the long run, they will be integrated into the on-site Warehouse Management System. The project team keeps an eye on all activities of Adam and Eve via the fleet dashboard.
The ROS-based MOV.AI Robotics Engine Platform provides the TUGBOT with its robot navigation and fleet management systems enabling it to autonomously operate. “The systems hold and update a map of their area of operation which they use to independently find their way. As soon as a TUGBOT detects an obstacle, it stops and waits until the lane is free again”, Stulert says.
The TUGBOT availability is affected by its relatively long charging time und Robosavvy has been working on the TUGBOT 2 that presents numerous improvements in comparison with the earlier version highlighting its cutting-edge wireless charging system that enables continuous operation for nearly eight hours with 25-minute charging. The TUGBOT 2 will be officially launched in May 2022 and Fiege will exchange its TUGBOTs currently in operation becoming the first company in Europe to implement the TUGBOT 2.
Man and maschine
Automation is an ongoing process at Fiege . In close co-operation with the LEAN Management Team, it is currently analysing how processes can be designed more efficiently in relation to the 7+1 types of lean process thinking (or in Japanese: Muda) – for example by avoiding unnecessary itineraries.
It is not about replacing humans, says Florian Greve, the operations manager in charge of the area where the autonomous robots are employed: “By providing this transport equipment the TUGBOTs handle trite and recurring tasks. This then frees our employees and instead allows them to add value to those process flows where human skills are indispensable.”